Engineering & Manufacturing Consultants
Six-E is a pioneering firm that merges materials science and engineering with manufacturing technologies to address quality issues in the production of high value engineering components.
With more than 14 years of hands-on experience on materials, residual stresses and manufacturing we are able to offer a wide range of expert professional services tailored for the manufacturing sector.
Advanced Residual Stress Measurement Techniques
Mapping of stresses with a wide rage of mechanical methods suitable for industrial scale components and any level of complexity.
Development of a Method of Manufacturing for metallic parts utilizing predictive modelling for residual stresses and distortion as per the intrinsic material behavior and process conditions.
Employment of thermal and mechanical stress relief methods coupled with process optimization through modelling to address issues with cracking and /or distortion.
Simulation of Manufacturing Processes
Control of Residual Stresses in Manufacturing
Our mission is to support and revitalise the manufacturing sector providing expert services in control of residual stresses and distortion which can increase the sustainability, productivity and competitiveness in manufacturing.
Six-E
Innovative Engineering Solutions for You
At Six-E, we have a very long track record of residual stress projects for a wide range of industries, which has enabled us to build and shape our offering to meet the industry needs and expectations. Our team is dedicated to delivering quality and impact maximising the outputs and benefits in every project.
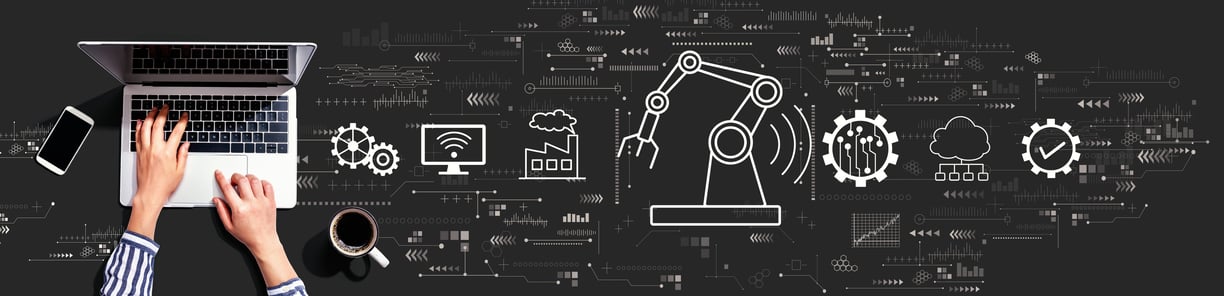
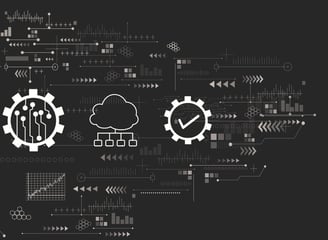
Your Trusted Engineering Partner
Expert Manufacturing Services
Due to our vast experience and unique capabilities, we can provide a complete service and solve the most complex manufacturing problems that lead to rejection of parts due to geometric or material non-conformances. We can help you assess and redesign your manufacturing process paving the way forward.
Industry focus
Sector specific knowledge and services
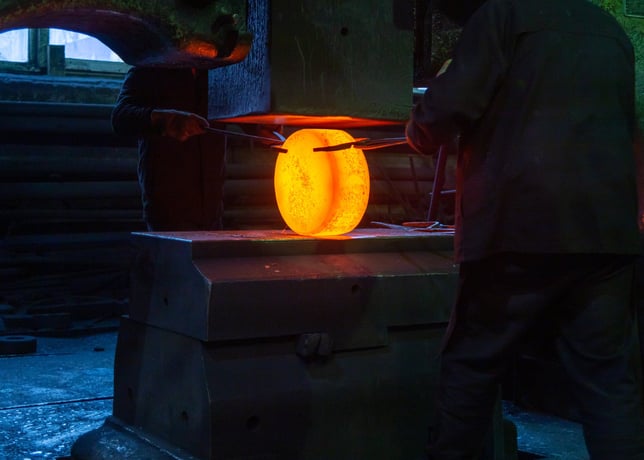
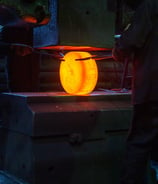
Machining
Machining is the process where we typically witness most of the cracking and distortion problems. The pre-existing stresses in the material are being released during the material removal steps, causing the part to move (throughout machining or after unclamping or both), ending with certain dimensions being out of tolerance. This is particularly troublesome for high precision machining. But pre-existing stresses is not the only source of distortion. Machining induced stresses, cutting forces and clamping conditions can alter how the part moves. Thus, quite often the stock material for final machining is not sufficient to achieve required dimensions and tolerances.
Designing machining strategies with respect to material removal sequence, clamping configuration, set-up changes etc. complemented by information on pre-existing and machining induced residual stresses will enable engineers to devise a right-first-time Method of Manufacturing.
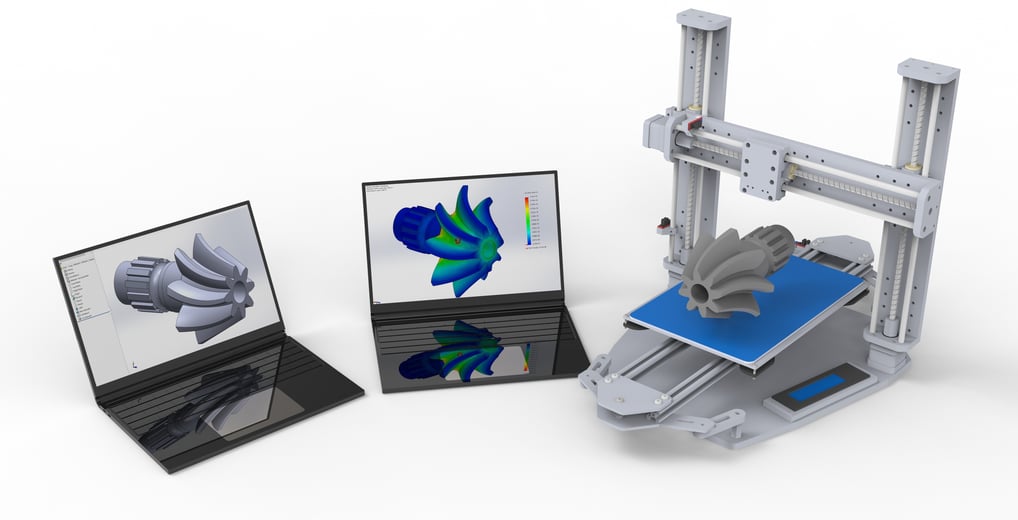
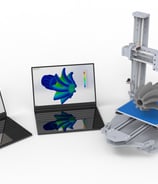
Additive manufacturing
From concept development to manufacturing based on Design for Manufacturing approaches
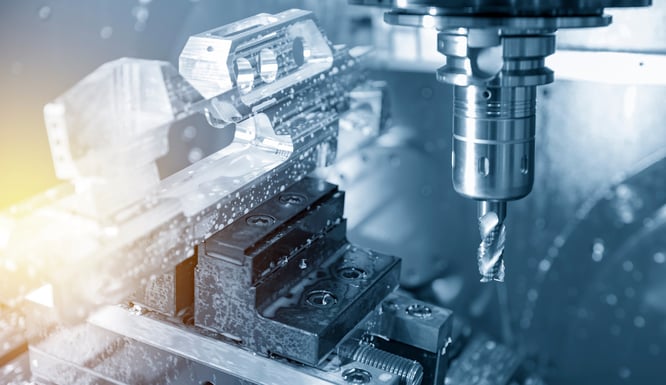
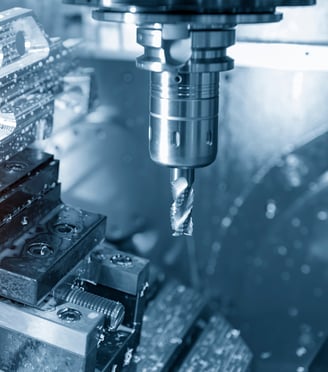
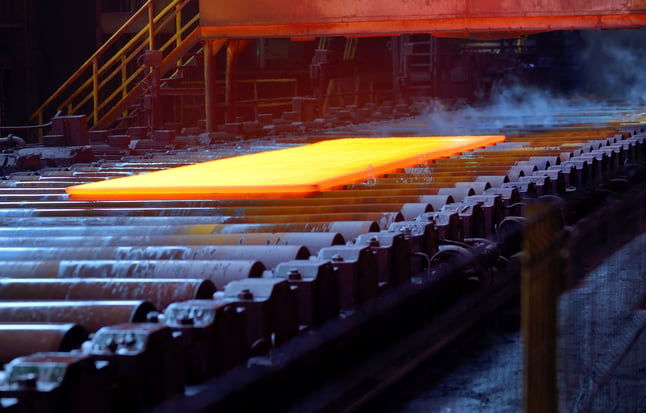
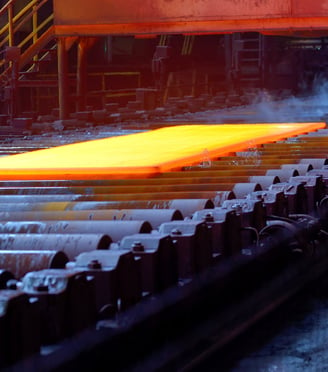
Heat-Treatments
Forging is rarely the primary source of residual stresses due to subsequent heat-treatments at very high temperatures. However, when forging is part of the manufacturing route, then it is considered together with the heat-treatments and quite often considerations about the geometry of the preform(s) dictate a number of different aspects in manufacturing. In some specific cases where parts are being heat-treated directly after forging, the pre-existing temperature and deformation fields can affect final residual stresses and observed modes of failure and/or distortion.
Forming on the other hand is a process that always cause non-uniform plastic deformation which inevitably lead to high residual stresses and springback. Though annealing stress reliefs may be employed to reduce stresses, the springback can lead to significant deviations from target geometry, which is very rare to recover considering subsequent machining steps.
In either case a more holistic approach is needed to address issues with distortion and/or cracking with experimental and modelling investigations.
Processes like quenching and other less intense cooling operations are an integral part of heat-treatments, but they can lead to significant residual stresses. These stresses could be reduced during subsequent annealing steps, but stress relief anneal is not always a viable option while stress will never be completely eliminated. Designing the heat-treatments as per material specifications, preform and final geometries, and employed manufacturing routes can lead to significant reduction of rejection rates due to cracking and/or distortion with huge savings in production costs.
Modelling the generation and evolution of residual stresses is they key to understand and link the manufacturing steps with the observed failure and /or distortion mode(s), complemented by targeted measurement plan.
Characterising the process conditions and their products is of outmost importance to establish a baseline scenario and propose any potential improvements.
Forging and Forming
Welding
Welding processes add localised heat and sometimes pressure to fuse parts together. The transient nature of the process with the high local temperatures and fast cooling rates cause severe residual stresses and distortion. These stresses can also be detrimental for the in-service performance of these parts. Their assessment has become a routine activity and all our measurement capabilities can provide a wealth of information.
Residual stresses and distortion can be managed with proper selection of process conditions and their optimisation through modelling. But in most cases it is unavoidable to use thermal or mechanical stress relief technologies to reduce their magnitudes. Suitable options depend on the nature of the application and their successful deployment require thorough design and careful consideration of the implications.
At Six-E we bring together the know-how and all the necessary skills to develop and deliver effective solutions for welding applications.
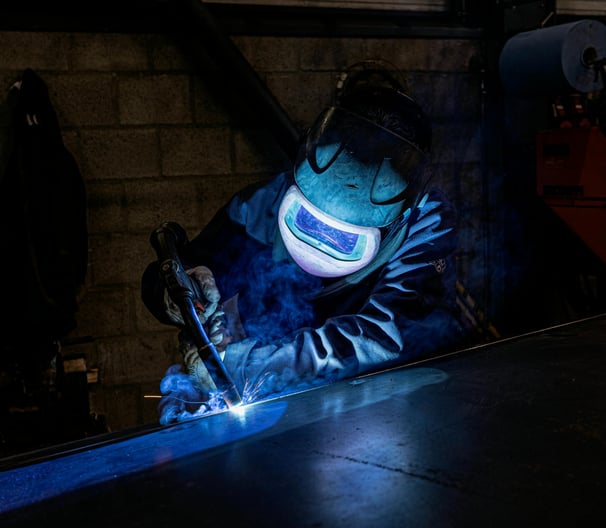
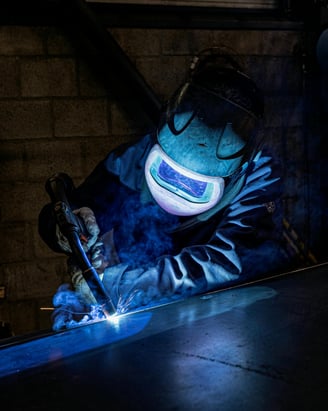
Client Feedback
Hear what our clients say about our engineering consultancy services.
The team at Six-E Engineering transformed our project with their expertise and dedication. Highly recommend their consultancy services for any engineering needs.
John Smith
New York
Six-E Engineering provided exceptional support and innovative solutions that exceeded our expectations. Their professionalism and attention to detail made a significant difference in our project outcomes.
Emily Davis
Los Angeles
★★★★★
★★★★★
Engineering & Manufacturing Consultancy
Expert engineering solutions for your business needs.
Services
Contact
+44(0)7502167793
© 2025. All rights reserved.